1. Step One: Smelting
Aluminum is made using electrolysis on an industrial scale and aluminum smelters need a lot of energy to run efficiently. Smelters are frequently located adjacent to major power plants due to their requirement for energy. Any increase in the cost of power, or the amount of power required to refine aluminum to a higher grade, increases the costs of aluminum coils. In addition, aluminum that has been dissolved separates and goes to a collection area. This technique also has considerable energy requirements, which impacts the aluminum market prices as well.
2. Step Two: Hot Rolling
Hot rolling is one of the most often used ways to thin an aluminum slab. In hot rolling, metal is heated above the point of recrystallization to deform and further shape it. Then, this metal stock is passed through one or more pairs of rolls. This is done to reduce thickness, make thickness uniform, and to achieve a desired mechanical quality. An aluminum coil is created by processing the sheet at 1700 degrees Fahrenheit.
This method can produce shapes with the appropriate geometrical parameters and material characteristics while keeping the metal volume constant. These operations are crucial in producing semi-finished and finished items, such as plates and sheets. However, finished rolled products differ from cold rolled coils, which will be explained below, in that they have less uniform thickness because of tiny debris on the surface.
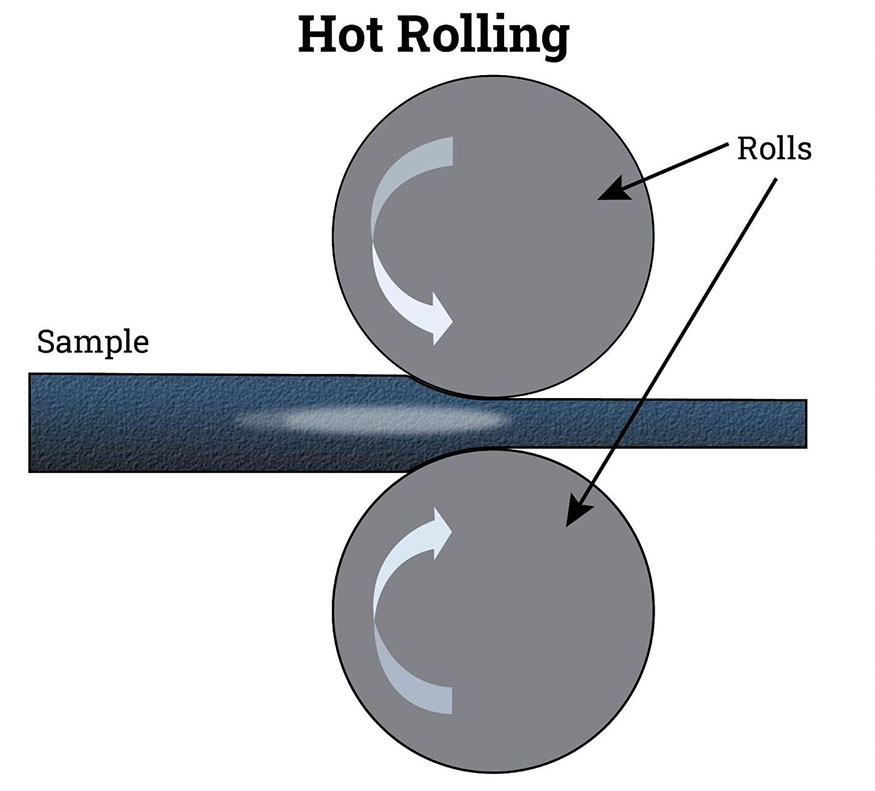
3. Step Three: Cold Rolling
Cold rolling of metal strips is a unique area of the metalworking sector. The process of "cold rolling" involves putting aluminum through rollers at a temperature lower than its recrystallization temperatures. Squeezing and compressing the metal increases its yield strength and hardness. Cold rolling occurs at the work-hardening temperature (the temperature below a material’s recrystallization temperature), and hot rolling occurs above the work hardening temperature- this is the difference between hot rolling and cold rolling.
Many industries use the metal treatment procedure known as cold rolling to produce strip and sheet metal with the desired final gauge. The rolls are frequently heated to help the aluminum be more workable, and lubricant is used to prevent the aluminum strip from sticking to the rolls. For operational fine-tuning, the rolls' movement and heat can be changed. An aluminum strip, which has already undergone hot rolling, and other procedures, including cleaning and treating, is cooled to room temperature before being placed into a cold mill rolling line in the aluminum industry. Aluminum is cleaned by rinsing it with detergent and this treatment makes the aluminum coil hard enough to withstand cold rolling.
After these preparatory steps have been addressed, the strips undergo repeated passage through rollers, progressively losing thickness. The metal's lattice planes are disrupted and off-set throughout the process, which results in a harder, stronger final product. Cold rolling is among the most popular methods for hardening aluminum because it reduces the thickness of the aluminum as it is crushed and pushed through rollers. A cold rolling technique can lower an aluminum coil's thickness by up to 0.15 mm.
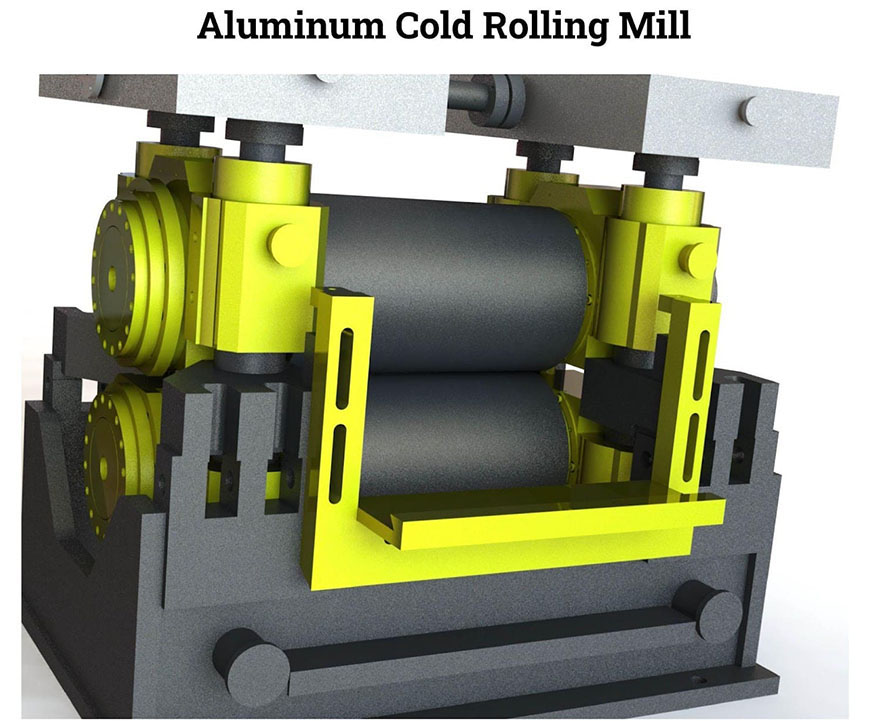
4. Step Four: Annealing
An annealing process is a heat treatment used primarily to make a material more malleable and less rigid. The decrease in dislocations in the crystal structure of the material being annealed causes this shift in hardness and flexibility. To avoid brittle failure or to make a material more workable for following operations, annealing is frequently done after a material has undergone a hardening or cold working procedure.
By effectively resetting the crystalline grain structure, annealing restores slip planes and enables further shaping of the part without excessive force. A work-hardened aluminum alloy must be heated to a specific temperature between 570°F and 770°F for a predetermined period, ranging from about thirty minutes to three hours. The size of the part being annealed and the alloy it is made of determine the temperature and time requirements, respectively.
Annealing also stabilizes a part's dimensions, eliminates problems brought on by internal strains, and reduces internal stresses that may arise, in part, during procedures like cold forging or casting. Additionally, aluminum alloys that are not heat-treatable can also be successfully annealed. Therefore, it is frequently applied to cast, extruded, or forged aluminum parts.
A material's ability to be formed is enhanced by annealing. Pressing or bending hard, brittle materials can be challenging without causing a fracture. Annealing aids in removing this risk. Additionally, annealing can increase machinability. The extreme brittleness of a material might result in excessive tool wear. Through annealing, a material's hardness can be decreased, which can lessen tool wear. Any remaining tensions are eliminated by annealing. It is usually best to reduce residual tensions wherever feasible because they might lead to cracks and other mechanical issues.
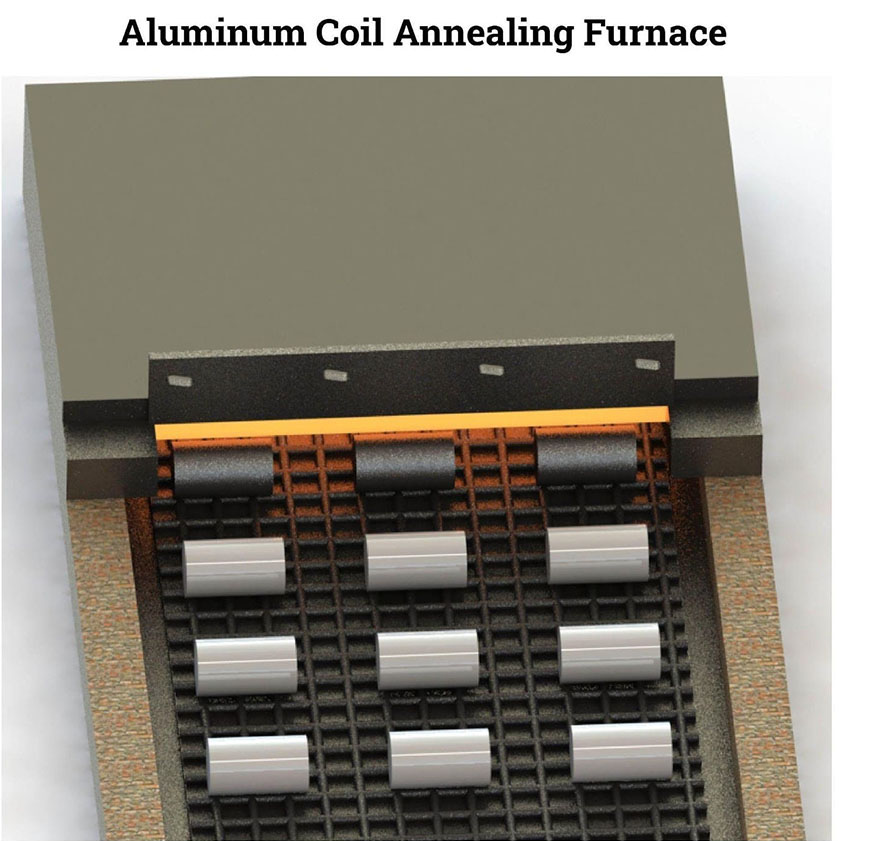
5. Step Five: Slitting and Cutting
Aluminum coils could be manufactured in one very long continuous roll. To pack the coil into smaller rolls, however, they need to be sliced. To perform this function, aluminum rolls are run through slitting equipment where incredibly sharp blades make accurate cuts. A lot of force is required to perform this operation. Slitters split the roll into smaller pieces when the applied force exceeds the aluminum's tensile strength.
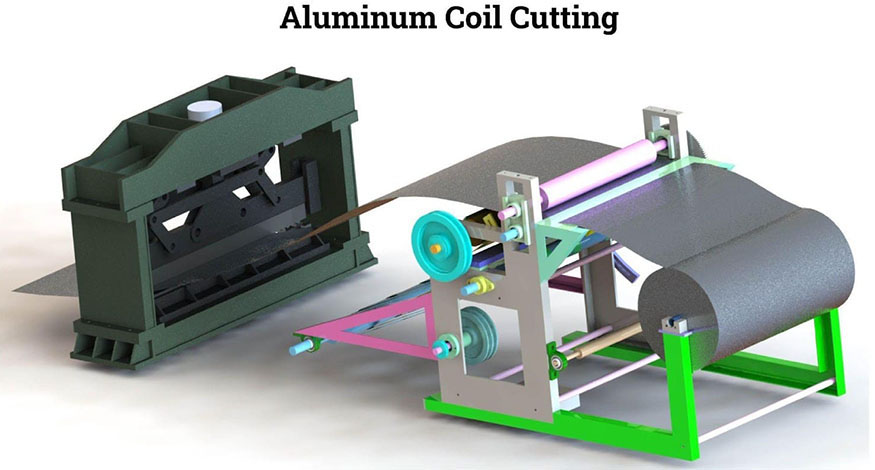
To start the slitting process, the aluminum is placed in an uncoiler. Afterward, it is passed through a set of rotary knives. The blades are positioned to obtain the best slit edge, considering the desired width and clearance. To direct the slit material to the recoiler, the material is subsequently fed through separators. The aluminum is then bundled and wrapped into a coil to prepare for shipping.
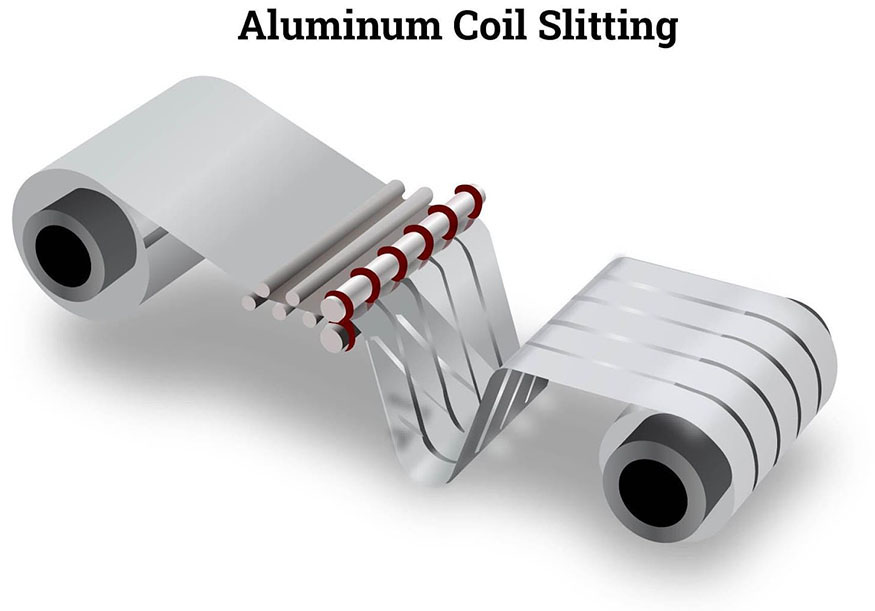
Jindalai Steel Group is the Leading Aluminum Company and Supplier of aluminum coil/sheet/plate/strip/pipe/foil. We have customer from Philippines, Thane, Mexico, Turkey, Pakistan, Oman, Israel, Egypt, Arab,Vietnam, Myanmar, India etc. Send your inquiry and we will be happy to consult you professionally.
HOTLINE: +86 18864971774 WECHAT: +86 18864971774 WHATSAPP: https://wa.me/8618864971774
EMAIL: jindalaisteel@gmail.com sales@jindalaisteelgroup.com WEBSITE: www.jindalaisteel.com
Post time: Dec-19-2022