Overview of 1050 Aluminum Disc/Circle
The most common used product is aluminum discs 1050, aluminum content must reach 99.5% above qualified products.due to the good toughness of aluminum circles in the 1050, it is suitable for stamping processing. 1050 aluminum discs are used to process kitchen utensils such as pan and pots, pressure cooker liner , and also widely used in reflector traffic sign, light etc.
Chemical Composition of 1050 Aluminum Disc/Circle
Alloy | Si | Fe | Cu | Mn | Mg | Cr | Ni | Zn | Ti | Zr | Other | Min.A1 | |
1050 | 0.25 | 0.4 | 0.05 | 0.05 | 0.05 | - | - | 0.05 | - | 0.05 | 0.03 | 0.03 | 99.5 |
Parameters of 1050 Aluminum Discs
Product | 1050 Aluminum Discs |
Alloy | 1050 |
Temper | O, H12, H14, H16, H18, H22, H24, H26, H32 |
Thickness | 0.4mm-8.0mm |
Diameter | 80mm-1600mm |
Lead Time | Within 7-15 days after receiving deposit |
Packing | High quality exporting wooden pallets or based on customer requirement |
Material | Using high-tech machinery utilizing premium grade Aluminium Coil. (Hot rolling/cold rolling).Customized according to the needs and demands of the clients these can be availed at different technical specifications. |
Surface: | Bright & smooth surface, dont have any defects like white rust, oil patch, edge damage. |
Application | Aluminum Discs are used in Reflective Sign Boards, Road Furniture,cooking utensils, Sand witch Bottom, non-stick cookware、for non-stick pan , pots, pans, pizza trays, pie pans, cake pans, covers, kettles, basins, fryers, light reflectors etc. |
Advantage: | 1. Alloy 1050 Aluminum Discs, deep drawing quality, good spinning quality, excellent forming and anodizing, no four ears; 2. wonderful reflectivity, good for Polishing; 3. Good anodized quality, suitable for hard anodizing and enameling; 4. Clean surface and smooth edge, hot rolled quality, fine grains and after deep drawing no loop lines; 5. Excellent pearl color anodizing. |
Process of 1015 Aluminum Disc
1. Prepare the master alloys.
2. Melting furnace put the alloys into the melting furnace.
3. D.C.cast aluminum ingot:make the mother ingot.
4. Mill the aluminum ingot: make the surface and side smooth.
5. Heating furnace.
6. Hot rolling mill:make the mother coil.
7. Cold rolling mill:the mother coil was rolled as the thickness you want to buy.
8. Punching process:make the size what you want.
9. Annealing furnace:change the temper.
10. Final inspection.
11. Packing:wooden case or wooden pallet.
12. Delivery.
Detail Drawing
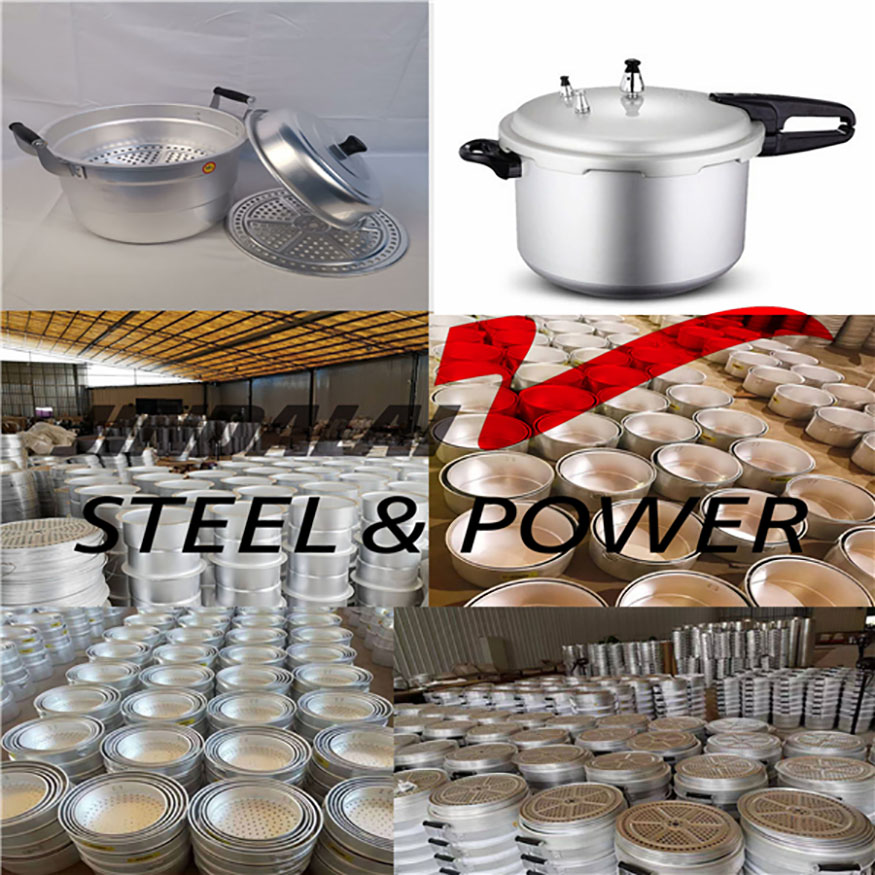